New laser scanning increases quality and reduces costs
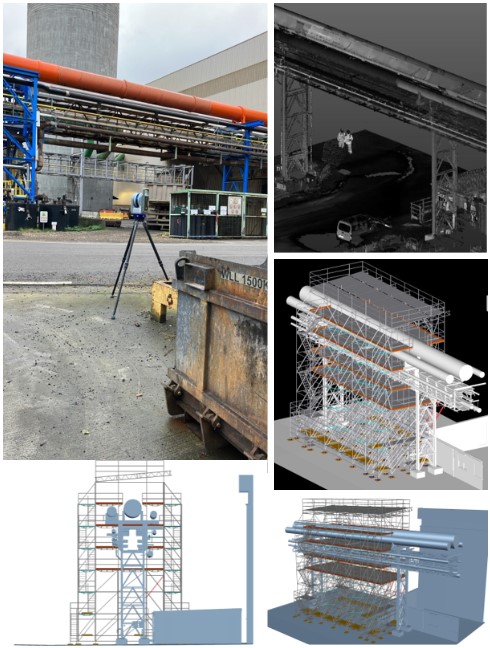
We have recently been allowed to add an innovative technique to our record of innovations. Our engineering department has already carried out several projects using laser scanning. Not only our team is delighted, customers are also experiencing the benefits.
Hard-to-reach pipeline needs maintenance
At ArcelorMittal, we were commissioned to build freestanding scaffolding structures on a piperack. Due to blasting operations, the scaffolding also had to be fully immersed and required a foreseeable load of 300kg/m². This made the calculation and assembly of scaffolding even more complex in terms of wind load and payload...
Astrid Schaut, Engineering Manager: "In the first phase, we worked in the traditional way. This meant that we first assembled the scaffolding and prepared the calculation note as-built (as assembled). This way of working was chosen because no plans were available from the piperack and its surroundings.
The consequence of this method is that we need several weeks of measuring and calculation work after assembly before the scaffolding can be released for use.
In the second phase, we performed laser scans to map the surroundings and all the details of the rack. This allowed us to design the scaffolding in advance. This has many advantages, both for us as a scaffolder, but also for the customer.
How a laser scan works
A laser scanner uses lasers to accurately map the environment. This involves emitting pulses of light at high speed that reflect off the object being scanned. The reflected laser beams are captured and converted into digital dots that combine to form a single point cloud and thus subsequent digital images.
"Laser scanning allows us to design and calculate the scaffolding "first time right". This results in the most economical scaffolding, which favourably affects assembly time, dismantling time and material utilisation. The scaffold can also be released for use immediately after assembly, which means a surplus for the customer. This shortens the process considerably and allows us to work more efficiently, more accurately and to deploy our people better". Astrid continues.
Project engineer Sebastiaan De Smet also explains: "Laser scanning works quickly and easily. We visit the site once and measure everything immediately. As a result, we have everything available digitally and simply cannot forget anything. The lead time is therefore shorter and more efficient than traditional measuring. Laser scanning is also accurate to a few millimetres whereas with traditional measuring, you are dependent on the person and the way the measurement is taken."
Needless to say, these benefits are a cheaper and sustainable solution for the customer, and several customers call on our experienced team to make the best use of the technology.
Team engineering:
Manager engineering: Astrid Schaut
Laser scan + calculation of scaffolding: Sebastiaan De Smet
Laser scan + design: Kevin Ongena